棱合的Additive Moulding™是一種具有新材料和設計範疇的自動化製造技術,開拓了各種不同產品應用的可能性。3D排列的連續纖維複合材料現在可以在復雜的形狀中使用,並且可以在單一零件中使用不同的材料組合。同時具有最大的性能和可擴展性
Additive Molding™
最大性能和可擴展性
性能
複合材料:3D應力對齊排列纖維提供最佳化的強度和剛性
設計: 最佳化的結構與材料運用效率
多功能:材料組合和高度整合的設計
埋入式元件:電子,電路和金屬組件
設計: 最佳化的結構與材料運用效率
多功能:材料組合和高度整合的設計
埋入式元件:電子,電路和金屬組件
+
可擴展性
經濟性:高產出, 高度自動化製程
多樣性:廣泛的材料選擇,成熟的全球供應鏈
外觀:高品質的成型表面和公差
適合量產:可重複性高的製程,高可靠度的設備
多樣性:廣泛的材料選擇,成熟的全球供應鏈
外觀:高品質的成型表面和公差
適合量產:可重複性高的製程,高可靠度的設備
Additive Moulding™ 如何運作
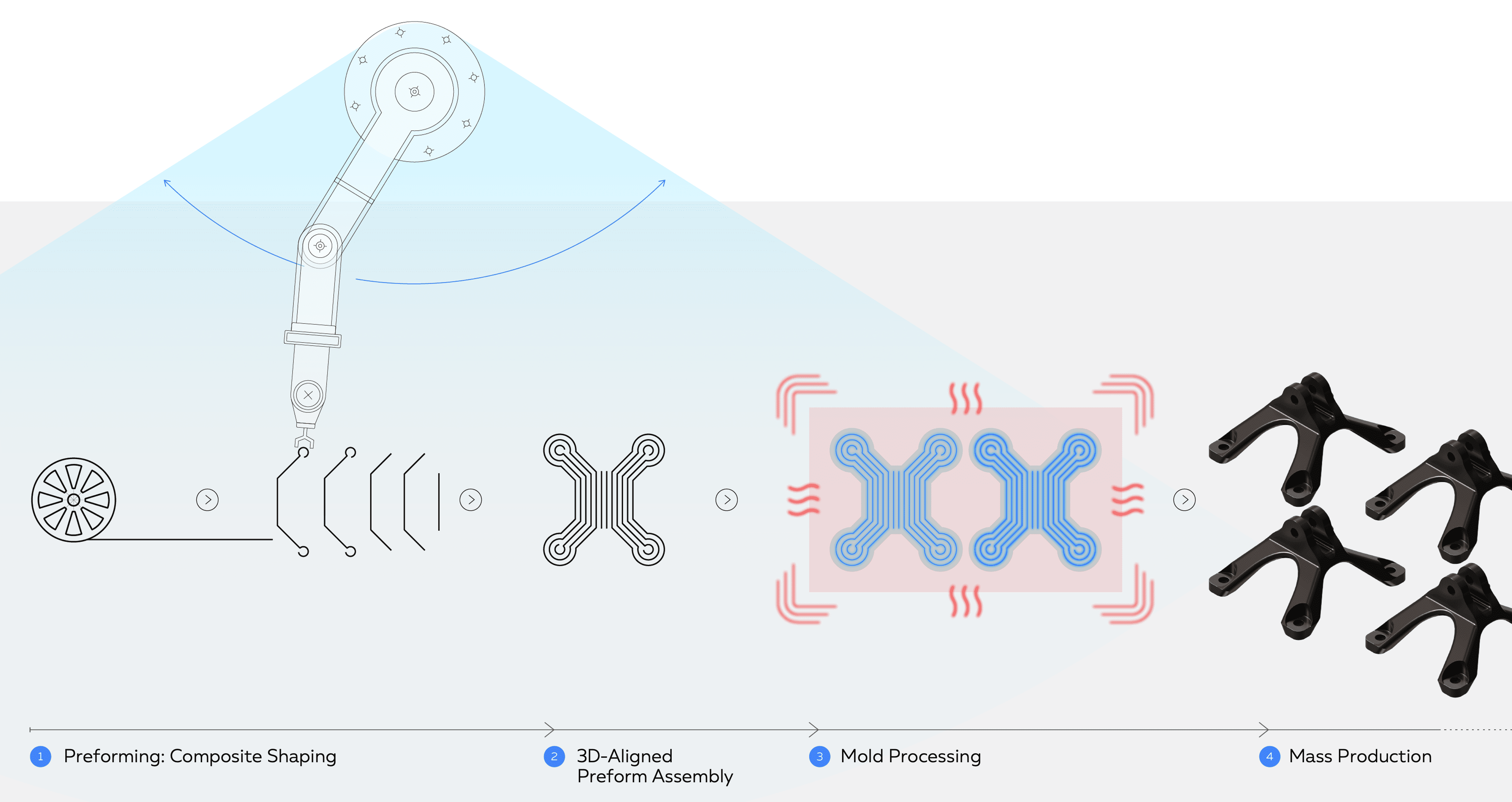
棱合擁有專利的Additive Moulding™技術以及高度自動化的積層製造和成型製程,可以將複雜的連續3D纖維排列(例如,碳纖維和玻璃纖維),熱塑性塑料和零組件(例如,電路,電子和金屬零件)整合成出色的產品
1
預成型:複合成型
連續的乾纖維與熱塑性樹脂浸漬後,預成型為最終產品的一部分。這些預成型的部件具有與產品3D應力向量對齊的連續複合纖維。
連續的乾纖維與熱塑性樹脂浸漬後,預成型為最終產品的一部分。這些預成型的部件具有與產品3D應力向量對齊的連續複合纖維。
2
3D對齊的預成型部件組裝
將所有預成型的部件組裝成最終的產品。
將所有預成型的部件組裝成最終的產品。
3
成型製程
最終成型製程將所有部件結合成具有完美性能,高精確性,出色的表面質量和零件間的高度可重複性。
最終成型製程將所有部件結合成具有完美性能,高精確性,出色的表面質量和零件間的高度可重複性。
Additive Molding™ 能為您的產品做什麼?
1
解析度與精度
在非常細小,複雜的特徵以及嚴格的半徑的範圍內,以精確地3D纖維排列,實現精準的公差。
2
表面外觀
無需其他後製程處理即可達成漂亮的A級表面。憑藉模具內部咬花設計和裝飾膜的功能,Additive Moulding™幾乎可以滿足任何表面外觀要求,並符合業界標準的射出成型規格。
3
多種材質
不著痕跡地結合不同的材料來達成多功能區域需求,例如RF訊號穿透窗口或依照不同位置優化的強度、剛性、熱傳遞和電性。
4
大型零件
可依據設計需求生產大型零件,滿足嚴苛的的結構應用需求。
5
製造規模
以先進的製造工藝與具有成本效益量產設計來滿足大規模的生產需求。
6
永續經營
透過高效率節能製造,可完全回收的材料以及前所未有的整個生命週期耐用性,重新定義環保與永續經營的標準。
已通過驗證的技術
複合材料製造,積層製造
高性能航太產品雖然率先使用複合材料和積層製造來定義高性能結構,但其大量生產的能力仍然受到許多限制。
+
快速成型
世界上產量最高的複雜零件製造工藝- 模具成型,以低製造成本提供了無與倫比的可量產性,但是歷史上一直沒有辦法滿足高性能應用材料的要求。
Additive Moulding™以世界領先的製造商所信賴並已通過驗證的技術為基礎,透過航太工業所開發的先進材料加工方法和無與倫比的設計能力提供了卓越的性能。Additive Moulding™ 運用業界成熟的模具成型方式,來達成兼具高度量產性以及高速生產的製造技術。
憑藉在材料科學,複合材料和熱塑性塑料加工方面的豐富經驗,棱合使世界一流領導品牌廠商能夠運用3D纖維排列與針對製程進行結構優化的設計來大規模生產創新,高性能,可持續的產品。
世界一流領導品牌的產品設計和工程團隊肩負著巨大的責任。為了不使他們的忠實客戶感到失望,必須更注重產品的可以量產性與品質。此外,產品性能和設計差異化亦是吸引新客戶和持續激勵現有客戶不可或缺的要素。Additive Moulding™為這些團隊提供了兼具量產、性能和設計的終極製造工藝。
與棱合合作
棱合的產品應用開發團隊具有跨領域的積層製造、複合材料製造與產品開發方面的深厚專業知識。這個世界一流的團隊配備了棱合強大的SpecificDesign™設計和優化軟件,專門致力於幫助客戶的產品設計團隊創造突破性的產品。
新客戶導入流程:
1
棱合設計和製造技術概述
2
透過對探索產品應用的討論來確認優先項目
3
協同合作產品設計工作
4
產品模擬與最佳化
5
樣品製作
6
全面量產
深入了解更多有關Additive Moulding™如何使您的產品與眾不同的資訊。
聯絡我們Related Posts
Arris Composites’ Additive Molding™ Carbon Fiber Truss Wins Red Dot: Design Concept 2020
More Details
Arris Secures $48.5M Series B to Accelerate Mass Production of High-Performance Carbon Fiber Products
More Details
CW Talks checks in with Ethan Escowitz, CEO of Arris Composites, to learn about the Additive Molding™ technology
More Details