Frequently Asked Questions: Ultra-Thin Capabilities
Erick Davidson and Trevor Forward answer some of the most frequently asked questions about the ultra-thin capabilities of Additive Molding.
One of the key advantages of utilizing Additive Molding for portable electronic devices (especially wearables) is the ability to create ultra-thin components that are lighter without compromising strength or stiffness. Product development teams, especially those focused on portable electronics, are leveraging this ability to reduce product weight or utilize the available space for greater product functionality, such as larger batteries.
Key Takeaways: Parts As Thin As 0.2mm with Advanced Composites
- Achieve wall thickness as thin as 0.2mm with matching or exceeding the stiffness, strength, and durability of heavier, thicker parts produced using conventional methods.
- Ultra-thin parts manufactured at ARRIS have out-of-plane features such as ribs, tabs, and posts that are connected to the base ultra-thin sheet with long, continuous fibers.
- Additive Molding is a practical and scalable method of bringing continuous composites to mass-produced products for increased performance.
Team Q&A: Ultra-Thin Capabilities
Check out the top six questions with answers below from ARRIS team members who get asked quite often about our ultra-thin capabilities. Need more information? Contact us directly to schedule a meeting with an applications engineer or request a sample part from our business development team.
- Erick Davidson is the Chief Engineer and Co-Founder of ARRIS. He leads many engineering functions at ARRIS including R&D tooling, thermal and structural simulation, mechanics of composites for part and layup design, and troubleshooting support on all customer programs.
- Trevor Forward is an Applications Engineer: Building on his knowledge in mechanical design, Trevor brings with him experience in consumer electronics, medical devices, and industrial applications.
How is ARRIS helping electronic device brands create thinner, lighter-weight parts without compromising durability or performance?
Erick: Our team can create ultra–thin structural composite parts that help brands save real estate and weight by matching or exceeding the stiffness, strength, and durability of heavier, thicker parts we are replacing.
Trevor: The brands I work with are focused on creating new product categories for their customers; this translates to the need for increasingly thinner and lighter parts to enable products with the smallest form factors possible without compromising on stiffness, strength, or durability. ARRIS has a unique ability to help our customers solve these problems with Additive Molding.
Explain Additive Molding and how the ARRIS team is able to create parts with wall thicknesses as thin as 0.2mm.
Erick: Additive Molding is a novel manufacturing method for composite parts that allows long, continuous fibers to be aligned to achieve the highest performance parts. Our method enables fiber alignment in just about any 3D shape, with the only real limitation being that the part is moldable. Ultra-thin parts are made possible by incorporating a sufficient amount of randomly oriented fibers to achieve strength and stiffness in any loading direction.
How do the ultra-thin capabilities of Additive Molding compare to other manufacturing processes such as machining or injection molding?
Erick: Typical ultra-thin parts manufactured at ARRIS have out-of-plane features such as ribs, tabs, and posts that are connected to the base ultra-thin sheet with long, continuous fibers. Machining such a part from metal would be challenging at best and require material removal and waste of up to 99% of the stock material. Injection molding would not be able to achieve the same thickness, and parts would be one to two orders of magnitude weaker and more compliant than an ARRIS part. Traditional compression molding would not be able to achieve similar fiber alignment, similar engineered performance, or similar feature complexity.
Trevor: Ultra-thin parts are a new class of parts altogether. Product teams are enabled to create parts too small for traditional injection molding processes while still achieving strength and stiffness comparable to metals.
What application types are benefiting from such thin continuous fiber composite parts? And why?
Erick: Many applications can benefit from high-performance thin composite parts. Examples include: small, complex, structural components in lightweight assemblies, structural covers over electronic components that enable more real estate for those components, rib and sheet structural components where the ribs provide stiffness and the sheet provides cover, radio transparent covers over antennas, and others.
Trevor: Often, we work with teams on applications where metal parts are replaced with lightweight continuous composites, or we’re replacing plastics with thinner, stiffer, and tougher parts. Product development teams can go even smaller than was ever possible using conventional methods without sacrificing strength or stiffness. Less wall thickness means more space for more important things like larger batteries, off-the-shelf antennas, flexes, etc.
What are the material options? And finishes, too?
Erick: Material options are composites comprised of carbon and/or glass fibers in a thermoplastic matrix. Currently, polycarbonate and bio-nylon are the available matrix materials but others are possible. Typical finishes are VDI-style textures and smooth polished finishes. Embossing and debossing of logos or text are also possible.
Trevor: The combination of Additive Molding with the materials we use can produce incredibly unique cosmetics; slight variation in every part gives each its own distinct fingerprint. That product differentiation really stands out.
What are the options for optimizing the performance of ultra-thin parts?
Erick: Many options are available for tuning the performance of an ultra-thin part that are not possible with other manufacturing methods. Within a single part, fiber alignment or loading can be altered in different regions to achieve differing levels of stiffness or to align with different loading directions. Within a single part, multiple material options are possible. For example, glass fiber can be used in specific regions where radio transparency is desired in an otherwise carbon part.
Want to meet with an ARRIS expert to discuss Additive Molding for your product? Start a conversation today, and request to schedule a discovery call with the team—use our contact us page!
Want to join the team and work with experts like Erick and Trevor? Consider a career at ARRIS at arriscomposites.com/join-us and be part of a fast-growing team that’s transforming how products are imagined, designed, and manufactured.
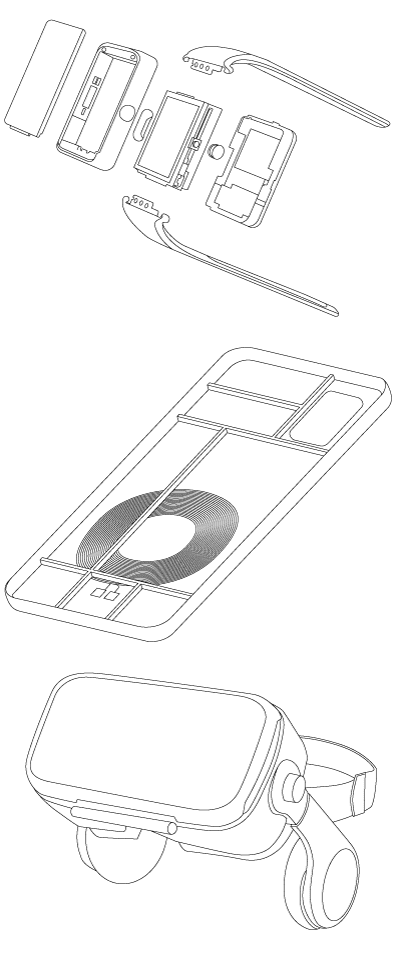