From Large-Scale Continuous Thermoplastic Composites to Mass Production
ARRIS' Additive Molding earns cover feature in JEC Magazine.
Carbon fiber composites are one of the highest-performance materials available, but you rarely see it leveraged in your everyday life unless you ride a high-performance bicycle, fly in an aircraft, or drive a Lamborghini. High-cost manufacturing processes such as hand layup and specialized automated systems have kept carbon fiber composites exclusive to niche applications.
Now, a new process called Additive MoldingTM, developed by ARRIS Composites, changes the underlying economics of optimized carbon fiber use. This mass-production technique creates aligned continuous thermoplastic composites at the cost and speed of molded plastics.
In Carbon Fiber We Truss
ARRIS Composites recently demonstrated the large-scale capability of its proprietary manufacturing technology with the production of an 8-foot, continuous-fiber truss structure, which won the prestigious Red Dot Design Concept Award 2020, recognizing quality and innovation.
Trusses are used in a broad range of applications where there is a requirement to efficiently support a load over a span of some distance by what is broadly referred to as a beam. Among efficient beams, like I-beams and H-beams, the truss is the ultimate in performance because it is a geometrically optimized structure. A truss can carry greater loads with the same amount of material or carry the same loads with less material and less weight. This is ideal for any structure that is moved by energy, as in the case of wind turbines, planes, trains, buses, and cars, all the way down to scooters.
While ubiquitous in buildings, trusses have seen limited use in these applications due to the high assembly and scrap costs associated with existing manufacturing processes.
Media Inquiries
media@arriscomposites.com
You can read the full article at JECComposites.com.
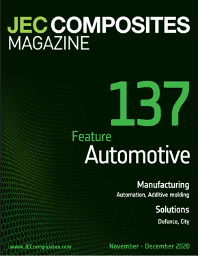