Benchmark Study of RF Performance in Advanced Composites Design
Multi-Material Composites for Multifunctional Design Processes of Radio Frequency Devices
Radio frequency (RF) characterization is an important aspect of designing components in close proximity to transmitting or receiving antennas. For components comprised of anisotropic composites, designing for RF functionality is particularly complex due to morphology and boundaries between the composite materials. Phenomena resultant from these material aspects greatly affect RF transmission and reception.
This paper discusses experiments conducted on ARRIS materials to characterize the RF response of multi-material composites with different fiber orientations. These results were compared to data available in literature and used to demonstrate an example of the design process. The performance of the redesigned ARRIS back case was compared to that of the standard plastic back case of a consumer mobile device, which served as the experimental control sample: Read Whitepaper /// Download PDF
The ARRIS Topology Optimized Case was Lighter & 3x Stiffer Than the Control While Achieving Comparable RF Performance
Exploring RF Performance in Multi-Material Composites
Numerous markets are adopting composites as a replacement for plastics and metals used by critical structural components, including unmanned aerial vehicles (UAVs), also known as drones, augmented reality (AR), or virtual reality (VR) devices, portable electronics, and wearable devices. A common motivation of these markets is to minimize the weight and volume of structural components and to maximize available weight and volume for electronics and supporting hardware systems. Reducing structural allocation must also meet the functional criteria of relevant application assemblies.
The Increasing Prevalence of Digital Communication Components Means RF Permittivity is a Functional Priority More Than Ever: In consumer and industrial electronics, applications benefit from structural components that possess the minimum viable weight while meeting mechanical and electronic hardware functionality criteria. A structural component’s corner-to-corner stiffness, for example, must meet a minimum value while constrained to only allocate material in regions free of electronics.
Mobile devices utilizing metal for structural backing, primarily aluminum, must incorporate gaps through which RF signals can be transmitted, as relevant metals drastically attenuate RF wavelengths. Such structural gaps are usually comprised of plastic, through which antennas can achieve connectivity. These gaps, however, present weakened interfaces that inhibit drop impact resistance and other mechanical performance requirements. To replace such metal casings, a monolithic backing without weakened antenna gap interfaces must provide equivalent RF functionality.
An Increasing Need Exists for Novel Processes Enabling RF Permittivity & Specific Stiffness in Portable Electronic Devices: By engineering RF and mechanical functionality into increasingly lightweight structural components, devices will become stiffer and lighter while still able to communicate across the networks they rely on. This study addresses this need by using ARRIS technologies, methods, and materials to simultaneously meet structural performance and RF functionality requirements at reduced weight in a redesigned back plate for a consumer or enterprise-level mobile device.
Want to schedule a call or meeting to discuss Additive Molding with an Applications Engineer? Start a conversation today using our contact us page!
Featured Q&A: Ryan Satcher and Trevor Forward on the Applications Engineering Team answer some of the most frequently asked questions about Additive Molding for portable electronics… Read Blog Post
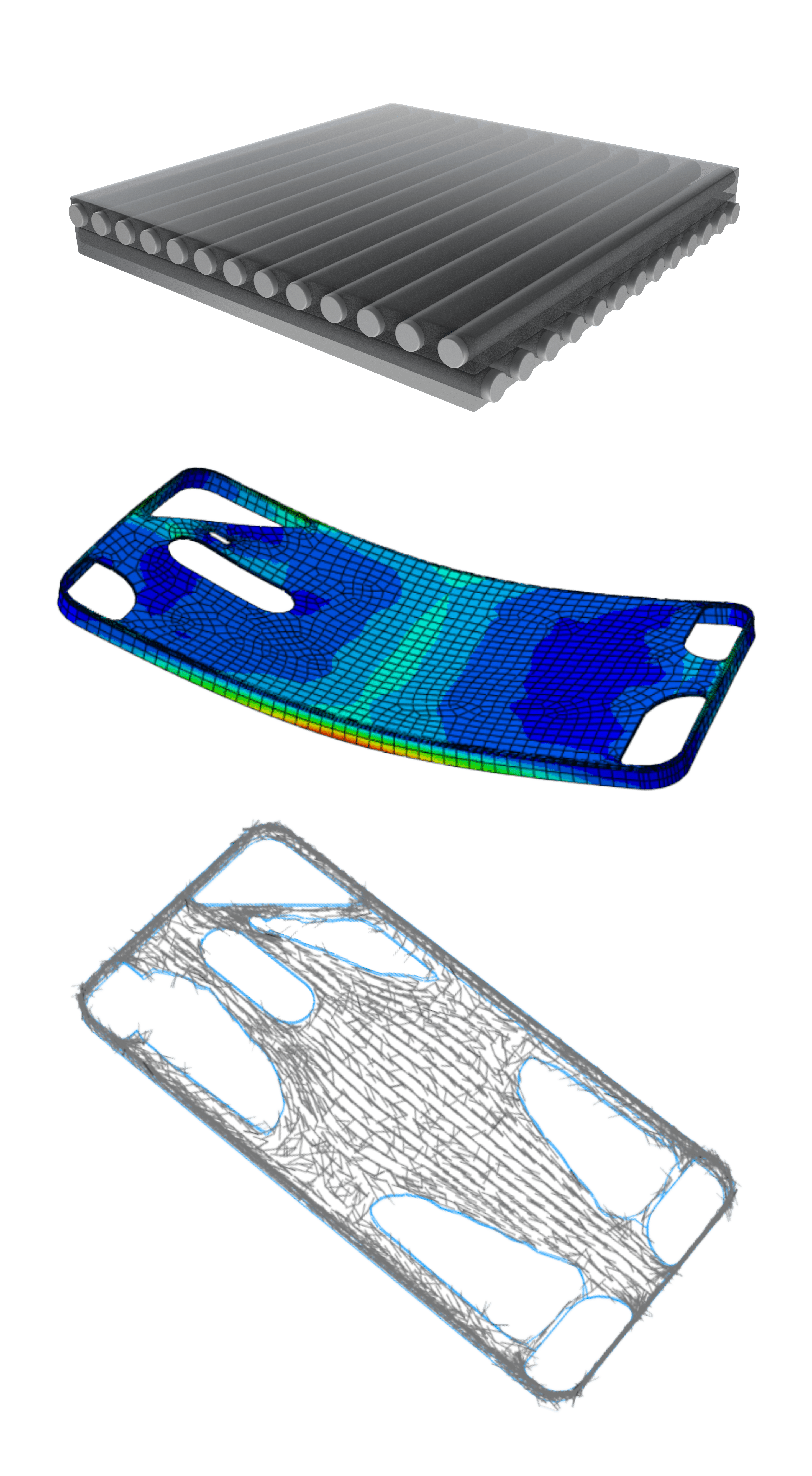