FAQ: Additive Molding for Bicycle & Cycling Products
Olivier D’Amours-Rousseau and Anja Riester on the ARRIS Applications Engineering Team answer some of the most frequently asked questions about Additive Molding for bicycle and cycling products.
Frequently Asked Questions About Continuous Fiber Thermoplastic Composites for Bikes
Additive Molding is utilized for bicycles and cycling products because the manufacturing and materials technology enables teams to create lighter yet tougher components with next-level performance not previously possible. Product development teams in this space already know the many benefits of carbon fiber composites, yet the need for greater design freedom and increased performance advantages is a must to meet ever-changing market demands.
Top 3 Advantages of Additive Molding Manufacturing
- 50-75% Weight Savings (Continuous Thermoplastic Composites vs. Metal Alternative)
- Improved Design Freedom & Greater Performance Advantages
- Scalability with Greater Sustainability (Near-Zero-Waste, Lower Energy, Bio-Based Material Options)
Check out these top questions with answers below from ARRIS team members who work closely with top bike brands. Need more information? Contact us directly to schedule a meeting with an applications engineer or request a sample part from our business development team.
- Anja Riester is a Senior Applications Engineer at ARRIS with a strong background in mechanical engineering and composite materials. She works directly with customers looking to leverage innovative technologies to achieve industry-leading performance, lightweighting, and sustainability advantages. Riester joined ARRIS in 2020 and is located in Berkeley at ARRIS’ headquarters.
- Olivier D’Amours-Rousseau is a Senior Applications Engineer at ARRIS focused on helping customers identify the right applications for Additive Molding. He leverages a comprehensive background in mechanical engineering and composites to help teams meaningfully leverage cutting-edge technologies for the redesign and optimization of parts that achieve unprecedented levels of performance. D’Amours-Rousseau joined ARRIS in 2019 and is located in Taiwan at ARRIS’ production facility.
Why are bicycle brands working with ARRIS?
Anja: It’s simple—extreme lightweighting, new design latitudes, and sustainability.
Olivier: Bike brands are always trying to push the limits of strength/stiffness-to-weight ratio and our technology can push those limits as no other existing manufacturing process can. Also, sustainability is extremely valuable to bike brands and that’s another advantage of our technology.
What is Additive Molding, and why are bike companies interested in this manufacturing and materials technology?
Olivier: Additive Molding is ARRIS’ proprietary technology which allows composite parts to be designed and manufactured in the most optimal way possible by aligning continuous fiber along the load paths. In other words, we are extracting the full potential from those orthotropic properties which make advanced fiber-reinforced plastics such high-performance materials. This results in structures having material only where it’s truly needed. No dead weight. This is obviously very compelling for bike brands. They can drastically reduce the weight of their existing components while matching or exceeding their structural requirements.
Anja: In addition to what Olivier said, sustainability is a notable aspect of Additive Molding, and that matters to the bike brands we are working with today. ARRIS is using thermoplastic resins, plus, our material options also include bio-based resins. The process itself is lower energy and near-zero-waste, so we can help teams achieve lower CO2 emissions.
What are the reasons behind the growing use of thermoplastic composites, especially in the sporting goods industry?
Anja: Environmental sustainability is a big topic among consumers. Thermoplastics are easy(er) to recycle or downcycle. The next step is using biodegradable resins, and the last step is combining those sustainable resins with biodegradable fibers for even greater sustainability (READ: FAQ on ARRIS Materials).
Olivier: As Anja pointed out, the bike brands we work with (similar to our footwear customers) are constantly looking for ways to reduce their carbon footprint. Using thermoplastic composites is already a great option because, unlike thermoset composites, they can be reprocessed and thus recycled into new products. In terms of performance, thermoplastic composites offer really good impact resistance, which can be a big advantage for some applications. Another benefit of thermoplastic composites is their shorter processing time which makes them well suited for large-volume production.
What kinds of bike components are ideal for Additive Molding? What should designers and engineers consider?
Olivier: Many bike components are great for Additive Molding but the most structural ones are typically ideal candidates (e.g., rocker links, saddle rails, shells, chainring and brake spiders, clamps, brackets, levers, faceplates, derailleurs, etc.). Some of the most ideal and compelling ones we see with customers are metal components because the lightweighting potential we’re able to provide is usually mind-blowing.
Anja: Oftentimes, we’re helping teams replace metal parts that have clear and defined load cases. Our material is highly anisotropic, and we get the greatest stiffness-to-weight ratio when we use this anisotropy to the max. In other words, our customers’ products benefit immensely from being able to place fibers only where and how needed.
How does Additive Molding compare to other processes typically used for bicycles and other sporting goods?
Anja: Conventional composite parts are made with sheet material or filament winding/pultrusion techniques that allow for continuous tubes or profiles. But imagine carbon fiber parts that look more like topology optimized structures or even complex castings. Those aren’t feasible with the typical processes used. That’s where we come in. Our parts are complex lattice structures. If those parts were to be made with other processes, lots of material would have to be removed while our process is near-zero-waste, and fibers are aligned with the greatest intention.
Olivier: The bike industry has been doing a great job using composite materials very effectively to push the limits of weight reduction throughout the years. But traditional composite manufacturing processes have inherent constraints limiting even the most experienced engineers to incremental performance gains.
For example, a laminate is made up of a sequence of plies at different orientations. Generally, each ply covers the whole area of the component which means that there is often a significant portion of every ply that doesn’t contribute much to the structural performance since the fiber isn’t oriented optimally. As explained above, Additive Molding allows us to align continuous fiber optimally along the load paths.
Another constraint of traditional composites is that laminates are typically limited to shell-like geometries which work just fine in some cases but are far from ideal in others. This is the reason why a lot of components are still metal. The complex 3D geometries that are possible with Additive Molding allow us to unlock tremendous performance for some structures. And this finally gives bike brands the option to switch from metallic components to composites.
In terms of production, traditional composites processes are slow and require a lot of manual labor—very inefficient and quality is inconsistent. Our automated Additive Molding process is much more efficient and consistent.
Why does sustainability matter to bike brands? How is ARRIS supporting these kinds of initiatives?
Olivier: As the population is becoming more and more environmentally conscious, there’s an increasingly strong pull from sporting goods end-users for more sustainable products and the bike sector is no exception. In addition to that market pull, some brands make sustainability a top company value. Thermoplastic composites can be reprocessed and thus recycled into new products.
Anja: Across all industries, sustainability is becoming more and more important. It’s a really common discussion our team has with customers in portable electronics, footwear, sporting goods, etc. Essentially it’s the end consumer who cares as well as governments who apply rules and restrictions. The bike industry is one of the industries trending towards much more sustainable products. Our technologies and materials allow teams to achieve their sustainability initiatives without having to compromise the highest level of performance their customers have come to expect of their brand. And we continue to innovate in these areas.
Want to meet with an ARRIS expert to discuss Additive Molding for your product? Start a conversation today, and request to schedule a discovery call with the team—use our contact us page!
Want to join the team and work with experts like Anja and Olivier? Consider a career at ARRIS at arriscomposites.com/join-us and be part of a fast-growing team that’s transforming how products are imagined, designed, and manufactured.
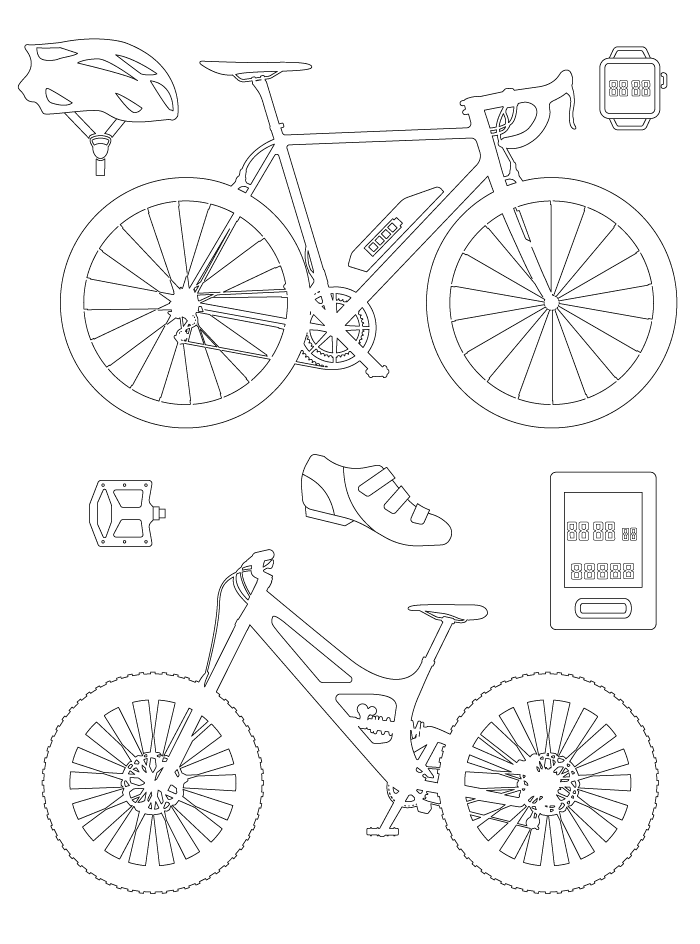