Q&A: Additive Molding for Performance Footwear
Michelle Callan on the ARRIS Business Development Team and Chief Engineer Erick Davidson answer some of the most frequently asked questions about Additive Molding for the footwear industry.
ARRIS partners with top brands to manufacture the highest performance footwear. Leading footwear designers are leveraging a first-of-its-kind manufacturing technology and materials to create 3D-optimized, continuous carbon fiber plates in ways not previously possible.
Top 3 Benefits of Additive Molding for High-Performance Footwear
- Enabling previously impossible designs with advanced composites to unlock next-level performance and visual innovation
- Maximum energy return and lighter than traditional plates—more optimized, 3D-aligned, continuous fiber with localized, tunable stiffness and strength
- Bio-based, PCR, and recyclable thermoplastic + lower energy, near-zero-waste manufacturing process
- With 17+ years of extensive experience, Michelle Callan creates footwear strategies that prove Additive Molding’s place in the footwear arena by translating what ARRIS does best in the world and how beneficial it is to product development teams.
- Erick Davidson is the Chief Engineer and Co-Founder of ARRIS. He leads many engineering functions at ARRIS including R&D tooling, thermal and structural simulation, mechanics of composites for part and layup design, and troubleshooting support on all customer programs.
Additive Molding for Footwear
Check out the top seven questions with answers below! Need more information? Contact us directly to schedule a meeting or request a sample part.
How is ARRIS helping companies level up footwear?
Michelle: Currently, with Carbon Fiber (CF) plates, this ability to fine-tune and design all regions of the plate is missing. Design freedom is almost non-existent. With Additive Molding, the design possibilities are practically endless. As an athlete, footwear is a big part of your equipment in virtually all sports. The footwear you get to choose is your connection to the ground. If ARRIS plates can make shoes lighter, more responsive, and stiffer in key areas, I would choose us! Athletes crave anything that gives them that edge. The technology that ARRIS has gives you this advantage.
Erick: We have a unique ability to increase the performance of footwear plates as measured by specific stiffness or specific strength. We have advanced simulation tools that allow us to simultaneously optimize the structural design and fiber paths. We are not limited by constant fiber directions inherent in traditional sheet-based composites. This enables us to trim weight by aligning continuous fibers only where needed. We can also easily vary the thickness over the footplate to further optimize performance based on the specific loading conditions.
What is Additive Molding, and why are footwear companies interested in this technology?
Michelle: In the most basic terms, Additive Molding is the ability to customize the structure down to the fiber level. Think of it as strong lego pieces that you can stack only where you want and, more importantly, only where they are needed.
Our ability to structurally place the CF only where it is relevant is a game-changer in the footwear industry. Not only is ARRIS reducing the amount of material needed, but we can fine-tune stiffness and strength throughout the plate while reducing weight. Recently we are taking this a step further and looking into fine-tuning each size to have the appropriate stiffness and performance attributes. More to come on that in the future!
Our sustainability story starts at the beginning of our process all the way to the end. We do as many simulations as needed to correct the performance targets before opening any tooling. Once the part is made, there is pretty much zero waste, and our part, in most cases, is fully recyclable. If these benefits weren’t enough, we significantly reduce the weight (because we use less material) while increasing performance. Currently, CF plates are incredibly wasteful, and most use non-recycled resin.
Erick: Additive Molding is a novel manufacturing method for composite parts that allows long, continuous fibers to be aligned to achieve the highest performance parts. It will enable fibers to align in just about any 3D shape, with the only real limitation being that the part is moldable. Footwear companies are interested because this technology allows for the highest performance parts, which is the top priority for many brands.
What types of footwear applications are ideal for Additive Molding? Any considerations for designers and engineers to know?
Michelle: Any application currently using a traditional composite is a contender. Anywhere the athlete wants to fine-tune performance is a perfect application. Parameters are specific to the application, and we work closely with the teams to understand any considerations that might be needed.
Erick: The ideal applications are those where performance as measured by specific stiffness or specific strength is the top priority for that component. The primary consideration is that the part is moldable.
How is ARRIS addressing the wants and needs of footwear product designers and engineers today?
Michelle: This is new to most designers and they are a bit stuck initially. We have developed design guidelines to get them started. We work closely with each project team so that everyone understands the benefits, timelines, and expectations during each step of the process.
Erick: With advanced simulation tools, we can use load data to help arrive at an optimized footplate design. The design freedom offered by our process allows these innovative designs to be realized.
What are the mass production capabilities of Additive Molding?
Erick: Mass production of footplates requires hard tooling for every size and shape of the footplate, so ramp up can take time—but once everything is in place, automation increases throughput and decreases costs.
What are ARRIS customers doing with Additive Molding that you’re most proud of in the footwear space?
Michelle: I can’t go into specifics on this one, but what I can say is that the ARRIS team is bringing something very compelling to the footwear space launching in SP24—an entirely different approach to CF on so many levels. I am thrilled to be a part of the innovative work at ARRIS!
Erick: I am most excited to see the increase in performance of our footplates which is just not possible with other traditional processes.
Why does sustainability matter in footwear? How is ARRIS making a real difference?
Michelle: No matter what industry you are in, sustainability is at the forefront. Footwear is no exception. The upper materials within footwear have almost completely switched to recycled materials with little to no expectations. Bottom units (which is what we fall into) are right behind. What ARRIS is doing is HUGE in terms of sustainability within the CF space. We have a near zero-waste process; we use less CF material combined with a bio-based nylon resin. We are not opening any molds until we know the design parameters are correct. No one else is doing this.
Erick: Sustainability is crucial to footwear customers. The ARRIS process is inherently more sustainable because it is a near zero-waste process, and due to the thermoplastic resins being used, the parts can be readily recycled. ARRIS also has an available Bio-Nylon resin and is working on developing other sustainable materials, including fibers.
Want to meet with Michelle to discuss Additive Molding for your product? Start a conversation today, and request to schedule a discovery call with Michelle and the team—use our contact us page!
Want to join the team and work with experts like Michelle and Erick? Consider a career at ARRIS at arriscomposites.com/join-us and be part of a fast-growing team that’s transforming how products are imagined, designed, and manufactured.
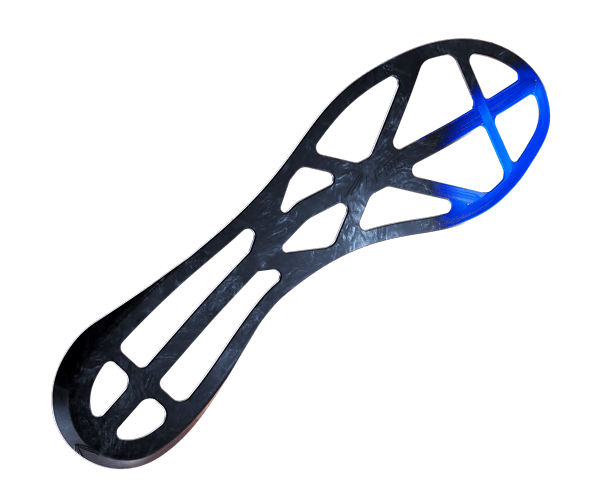