High-Performance Natural Fiber Composites (Flax)
Natural fibers have the potential to bring sustainability benefits to the composites industry through their adoption as high-performance materials.
This paper presents mechanical testing results of an ARRIS-designed natural fiber thermoplastic composite in comparison to similarly produced glass and carbon fiber-based materials.
- ARRIS produced a flax fiber reinforced composite with Additive Molding that competes with similarly produced glass fiber reinforced material in stiffness.
- The flax fiber reinforced composite by ARRIS is not only more than 500% stiffer than the neat polymer but also exceeds the stiffness-to-weight performance of the glass fiber composite.
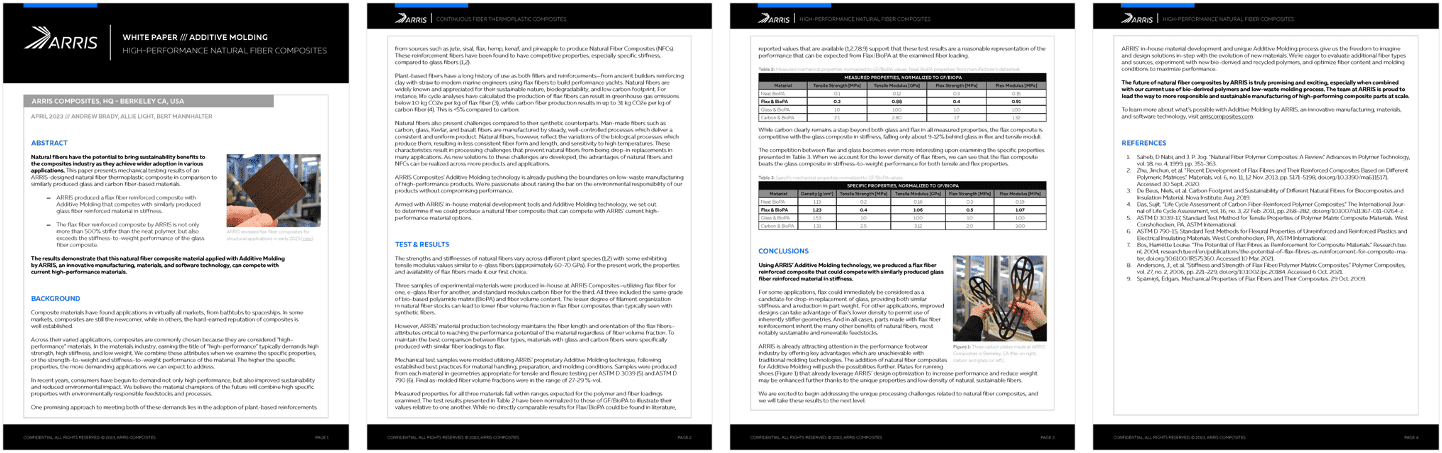
The results demonstrate that this natural fiber composite material applied with Additive Molding by ARRIS, an innovative manufacturing, materials, and software technology, can compete with current high-performance materials… Read Whitepaper /// Download 4-Page PDF
BACKGROUND
Composite materials have found applications in virtually all markets, from bathtubs to spaceships. In some markets, composites are still the newcomer, while in others, the hard-earned reputation of composites is well established.
Across their varied applications, composites are commonly chosen because they are considered “high-performance” materials. In the materials industry, earning the title of “high-performance” typically demands high strength, high stiffness, and low weight. We combine these attributes when we examine the specific properties, or the strength-to-weight and stiffness-to-weight performance of the material. The higher the specific properties, the more demanding applications we can expect to address.
In recent years, consumers have begun to demand not only high performance, but also improved sustainability and reduced environmental impact. We believe the material champions of the future will combine high specific properties with environmentally responsible feedstocks and processes.
One promising approach to meeting both of these demands lies in the adoption of plant-based reinforcements from sources such as jute, sisal, flax, hemp, kenaf, and pineapple to produce Natural Fiber Composites (NFCs). These reinforcement fibers have been found to have competitive properties, especially specific stiffness, compared to glass fibers (1,2).
Plant-based fibers have a long history of use as both fillers and reinforcements—from ancient builders reinforcing clay with straw to modern marine engineers using flax fibers to build performance yachts. Natural fibers are widely known and appreciated for their sustainable nature, biodegradability, and low carbon footprint. For instance, life cycle analyses have calculated the production of flax fibers can result in greenhouse gas emissions below 1.0 kg CO2e per kg of flax fiber (3), while carbon fiber production results in up to 31 kg CO2e per kg of carbon fiber (4). This is <5% compared to carbon.
Natural fibers also present challenges compared to their synthetic counterparts. Man-made fibers such as carbon, glass, Kevlar, and basalt fibers are manufactured by steady, well-controlled processes which deliver a consistent and uniform product. Natural fibers, however, reflect the variations of the biological processes which produce them, resulting in less consistent fiber form and length, and sensitivity to high temperatures. These characteristics result in processing challenges that prevent natural fibers from being drop-in replacements in many applications. As new solutions to these challenges are developed, the advantages of natural fibers and NFCs can be realized across more products and applications.
ARRIS Composites’ Additive Molding technology is already pushing the boundaries on low-waste manufacturing of high-performance products. We’re passionate about raising the bar on the environmental responsibility of our products without compromising performance.
Armed with ARRIS’ in-house material development tools and Additive Molding technology, we set out to determine if we could produce a natural fiber composite that can compete with ARRIS’ current high-performance material options… Continued: Download White Paper (with references)
Popular Posts
- Forbes Interview by Jim Vinoski: The ARRIS-Brooks Partnership and The Testing of A New Cutting-Edge Shoe At The Boston Marathon [ READ ]
- ARRIS Unveils Structural Flax Fiber Composites: The Advanced Manufacturer is Developing Natural-Fiber Composites with High-Performance Capabilities [ READ ]
- ARRIS Signs CM, Increasing Additive Molding Production Capacity To 1M+ Parts: Major Milestone in Scaling Advanced Composites for Mass-Market Products and Industrial Applications [ READ ]
Want to schedule a call or meeting to discuss Additive Molding with an Applications Engineer? Start a conversation today using our contact us page!
White Paper: Benchmark Study of RF Performance in Advanced Composites Design… READ
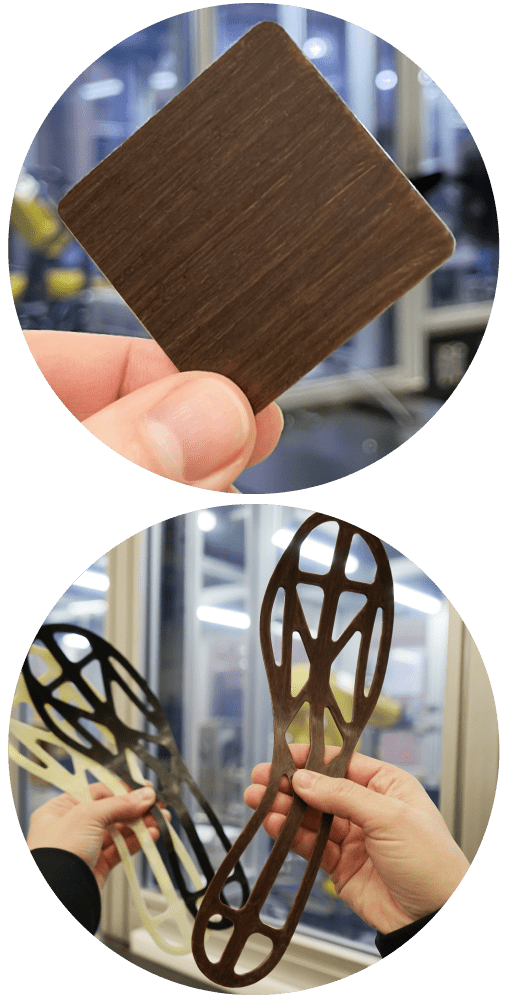